Stop 1
Lobby
Our Greene, New York, factory tour begins in the lobby. This is our largest facility (425,000 square feet) and is where the majority of our nearly 3,000 employees work. However, our footprint includes two additional factories (located in East Syracuse, New York, and Muscatine, Iowa) and over 100 Solutions and Support Centers in North America.
close
close
Stop 2
Office
At first glance, you’ll see a wall filled with pictures. Look deeper. You'll see the history of our innovation, our patents and our values. All united by one mission – to help our customers to run better and manage smarter.
close
close
Stop 3
Training
Here we teach employees about Raymond Lean Management (RLM). These procedures and techniques allow us to standardize work, track KPIs and make continuous improvements to ensure the best possible solutions. Our kaizen area helps generate continuous improvement by suggesting small incremental improvements (kaizens) to help optimize the operation. Nearly 1,000 kaizens have been submitted.
close
close
Stop 4
MANUFACTURING FLOOR
Take a look around and take it all in. This is where fabrication, welding, painting and assembly bring what was once a rendering to reality. Let’s make a forklift truck.
close
close
Stop 5
Fabrication
Here we use the latest technology and machinery to cut, bend and assemble steel. Our facility receives approximately 235,000 pounds (118 tons) of steel each day to support the manufacturing of material handling equipment. Each metal sheet is 5x10 feet and less than 0.500 inch thick.
close
close
Stop 6
Welding
This is home to over 150 welders and is the largest welding department in New York state. We use welding instead of other techniques because it builds a strong, sound structure. Fun fact: Each year, we hold a welding competition where the winner earns a trip to Japan to compete in the Toyota Material Handling Group (TMHG) Skills Competition, where multiple Raymond welders have been awarded a gold medal.
close
close
Stop 7
Paint
Who said high-tech machines can’t look pretty? We use a three-powder coat paint system plus one wet paint system for an end product that is durable, scratch-resistant and environmentally friendly. And of course, beautiful.
close
close
Stop 8
Assembly
This is where we take individual components and build them into a finished product. It’s complicated, but we use technology to simplify and improve the process. With our 5S system, we built a lean workspace for maximum productivity and efficiency. Here are the steps: sort, set in order, shine, standardize and sustain. This makes it easy for everybody to do their jobs.
close
close
Stop 9
Finished Truck
This is it. The assembly is over. The inspection is finished. And there you have it, folks. A massive 4,000-pound lift truck, ready to be shipped. But this end is really just the beginning. After leaving the factory, our lift trucks go on to help customers in warehousing, distribution and beyond.
close
close
Stop 10
On to the Solutions and Support Centers
After trucks are completed, they are shipped to our network of Solutions and Support Centers, located throughout North America. Through our Solutions and Support Centers, customers buy our lift trucks and get help with ongoing maintenance and support. If you would like to learn more about our products and services, please visit raymondcorp.com.
close
close
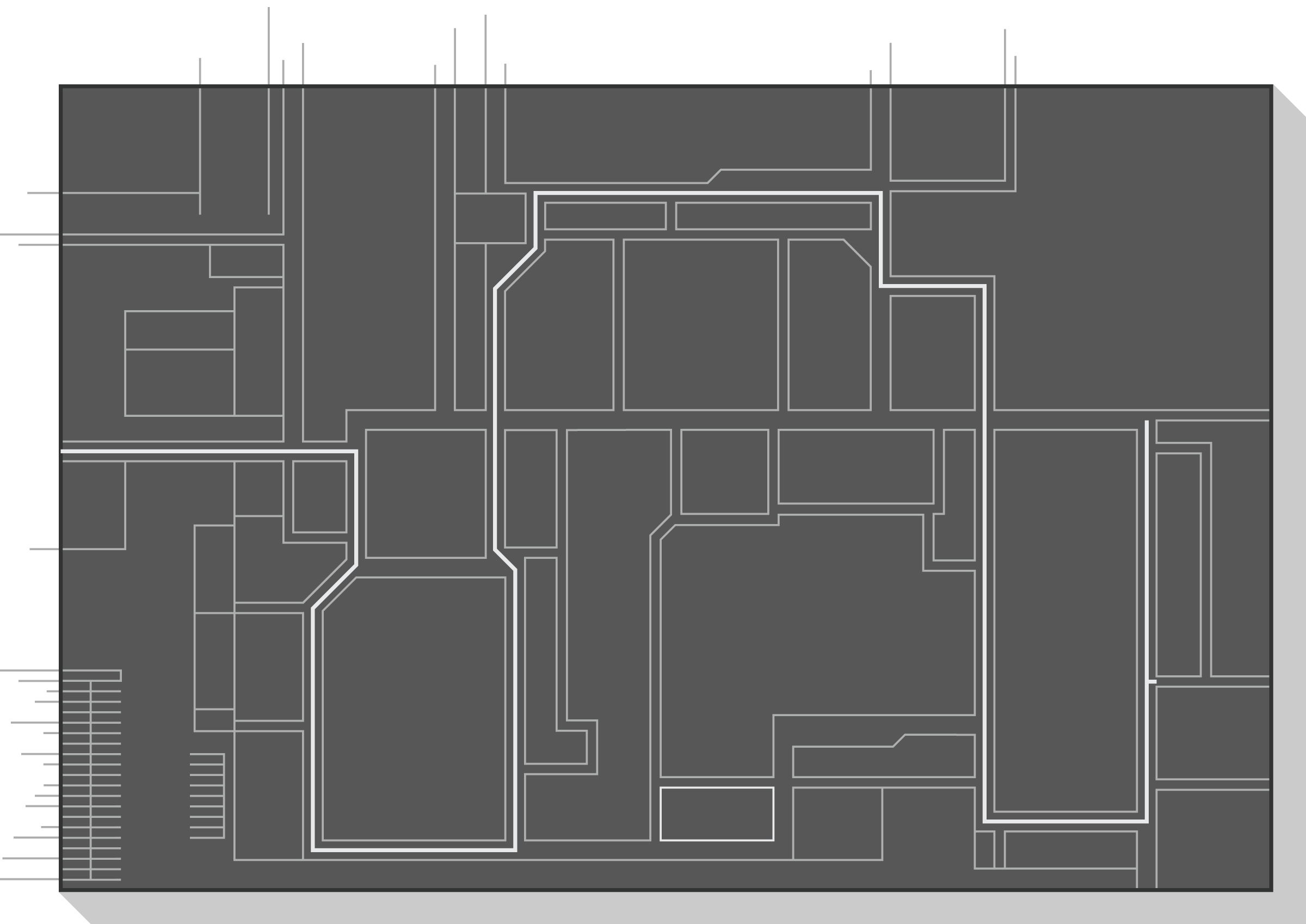
Click the red dots to see how we build forklifts.